|
Общее обозрение, модели,
оборудование Я уже
достаточно давно делаю ножи, но так редко
встречаются профессионалы среди потребителей ,
что практически каждому человеку приходится
обьяснять, как их надо править,почему правильно
сделаный нож не надо точить, как должен быть
изготовлен нож, чтобы к нему можно было применить
термин "самозатачивающийся", что некие
разводы на клинке - вовсе не дефект стали, а
даже наоборот... Весь материал подготовлен мною
для доступного чтения и никак не претендует на
какую-либо научность или "академичность".
Напротив, я постарался рассказать обо всем в виде
баек и небольших советов. Рассказывать Вам об
этом мне было не так сложно, все это я пропустил
через свои руки, поскольку литературы по
подобной тематике в продаже нет. Есть, конечно,
различные статьи, книги, но вот, чтобы сразу, в
одном месте о каких-то неосвещенных проблемах
для ножедела, о каких-то тонкостях, советах... Все
разбросано по отдельным островкам...
Поднабравшись маленько опыта, я хочу помочь тем,
кто в силу любых причин хочет сам сделать себе
разделочный или какой другой нож, но, в силу тех
же причин, вынужден общаться с дилетантами от
"ножедельства".
Сам я себя
"профессионалом" стал считать где-то лет
семь, поскольку "ножедельство" стало моей
профессией, и на хлеб для своей семьи я получаю от
того, что сделаю и как. Жизнь и практика, только
они способны дать действительную оценку вашего
труда. Кто-то рассуждает о преимуществах
какого-либо ножа и судит о нем по "внешнему".
Но и рассуждения его "внешние". Мне, например,
яркость блеска полировки стали вовсе не говорит
ничего о качестве самой стали, но говорит об
отношении мастера к своей работе. Насколько он
уважает то, что сделал. И, в то же время, матовый
поперечный штрих тонкой шлифовки говорит мне
о профессионализме того, кто приложил руку к
клинку. Девяносто процентов людей пройдет мимо
ножа с невзрачной, ромбовидной рукоятью и
двенадцатисантиметровым клинком и не
остановятся. Десять же, только взглянув, скажут:
"Добрый нож!". Среди этих десяти буду
находиться и я, и те, для кого нож - это
инструмент прежде всего. Надеюсь, среди этих
десяти будете и Вы. Мяснику и раздельщику,
охотнику- любителю и охотнику-промысловику
все равно, по каким технологиям изготовлен
клинок, по средневековым, первобытным, или
суперсовременным. Ему необходимо, чтобы нож
резал как можно дольше и был удобен в работе. Вот
здесь он всегда прав. В своих рассуждениях и
беседах с людьми я довольно часто применяю
словосочетание "создание ножей", и многие со
мной согласны. Как правило, это люди, которые уже
попробовали приложить какие-то усилия в
изготовлении и уже имеют какой-то опыт в создании
ножевого изделия. Попытаюсь обьяснить Вам, как
самостоятельно изготовить хороший нож, благо
обучение нашим законом не запрещено. Для
"скоростного" обучения Вам необходимо
прочесть эту страницу и - в добрый путь.
Посмотрим на рисунок. Вот так Вам придется
"снять" лишний металл, чтобы получилась
простейшая конструкция клинка. Черный контур -
контур заготовки на срезе. Красный контур -
готовый контур. Розовая заливка - "тело
клинка". Серая заливка - это то, что не нужно.
Таким образом, вы сможете изготовить любое
ножевое изделие с ограниченными свойствами, будь
то кухонный или хозяйственный нож. Чтобы создать
функциональное изделие, Вам придется прочитать
по крайней мере все то, о чем будет сказано далее
и просидеть не один день за наждаком... И это
МИНИМУМ!!! Но не пугайтесь!!! Даже если вы и не
хотите создавать ножи я постараюсь , чтобы вам
было интересно , а может быть Вы узнаете для себя
что-нибудь новенькое...
ОБОРУДОВАНИЕ. Прежде
всего хотелось бы предупредить, что собирать
все множество аппаратуры вовсе не обязательно.
Можно выбрать какую-нибудь модель и спокойно
выполнить всю работу на минимуме оборудования.
Поверьте мне, я начинал с одного мотора мощностью
2,2 квт. Но про минимум мы еще поговорим, а пока... На снимке вы видите
абразивный круг диаметром 300мм, толщиной 40мм;
посадочное место диаметром 76мм. Обороты должны
быть небольшие: 1200-1400 об/мин. Перед работой, в
целях безопасности, круг необходимо минут 15
прокрутить вхолостую, затем алмазным карандашом
или корундом выровнять до минимального биения.
Все ограничители необходимо убрать. Доступ к
кругу должен быть как можно свободнее. Вам
необходимо иметь возможность прижать заготовку
под любым углом, чтобы снимать металл там, где вам
надо, а не там, где этого "хочет" наждак. Для
отдельного вида работ должен быть подобран свой
круг. Для древесины - мягче, для стали - тверже. Я в
основном использую такие параметры круга:
габариты 300х40х76, твердость- СМ1/СМ2, зерно -
25А40П. Средняя стоимость - 10$, в зависимости, где
приобретаете и у кого... Приобретаю в основном
круги Лужского завода. Московский Абразивный
завод тоже выпускает неплохие круги, но как-то
не лежит душа, хотя за неимением "Луги" и его
изредка пользую... Потребуются вам и войлочные
круги. При ножевом изготовлении их необходимо
иметь много и разного диаметра. Приобретались
они мною уже давно, в магазине "Сделай сам",
по 55-ти рублей (застойных) за штуку. Вам надо иметь
приблизительно 5 больших кругов, диаметром от
250мм до 400мм, оптимальный вариант - 300мм. И,
желательно, множество маленьких разнообразных
диаметров, толщин и конфигураций. Изготовлялись
войлочные круги на валяльных комбинатах (была на
круге какая-то этикеточка), и купить вам их
придется только один раз. Они практически не
расходуются. Сейчас приобретается все это дело
на московском "птичьем рынке". Даю эту
информацию,чтобы при желании что-то сделать вам
много не пришлось бегать в поисках
необходимого... Отдельный вопрос - подготовка
войлочных кругов к работе. Самое неприятное -это
"центровка". На рисунке вы
видите вал полировальной бабки с войлочным
кругом. 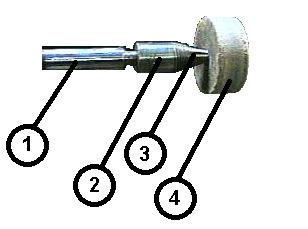
1.Сам вал.
2.Оправка с конусной резьбой (далее будем назывть
ее - морковка).
3.Насадочная резьба.
4.Полировальный войлочный круг .
Так вот, главная задача - это сделать посадочное
место в центре круга. Но, как бы вы его точно не
определили, все равно на валу при вращении
круг будет "бить". Чтобы максимально убрать
биение, я поступаю так:
1.Нагретым до красна стальным прутком (в кузнице
или у сварщика), я выжигаю конусное отверстие с
наружным диаметром 10мм и внутренним где-то 30-35 мм.
Затем обмазываю столярным клеем, и, когда клей
подсохнет, туго накручиваю на смазанную
вазелином или растительным маслом
"морковку". Появляется резьба посадочного
места. Далее, клей засыхает и круг готов к
"обдержке".
2.Из напильника изготавливаю резец, хотя можно
использовать любую закаленную пластину.
3.Накручиваю круг на "морковку", но уже не
туго, а слегка, чтобы он только сел посадочным
местом. Потом, при нажатии на круг резцом, он сам
закрутится до необходимого предельного момента.
4.Подобно токарю начинаю обтачивать круг до
минимального биения. Это относится к
полировальным кругам. Потому, что кроме
нанесения на них полировальной пасты
предварительной работы больше нет. Другое дело -
шлифовальные и доводочные круги. Для их
подготовки потребуются еще несколько операций.
Продолжим...
5.После обдержки на "морковке" промазываем
рабочую поверхность круга столярным клеем, даем
просохнуть и опять обдерживаем на морковке.
После промазки клеем необходимо обдерживать
круг по одной простой причине - круг
"ведет". Как бы вы ни старались, а клей свое
"дело" сделает, и после промазки и просушки
круг, как ни в чем не бывало, опять будет
"подбивать".
6.Последняя операция. Намазываем столярный клей и
накатываем необходимое абразивное зерно. Круг
готов. Теперь при отделочных операциях, у вас не
"отвалятся" руки при частой смене кругов.
Достаточно одного движения для скручивания, и
круг сам "слетит" с "морковки".
Набросили другой, и он сам при работе закрутится
до предельного значения.
ВНИМАНИЕ!!! Круги
диаметром более 200мм на "морковку"не сажать -
РАЗОРВЕТ!!! Только на посадочное место наждачного
круга!!! Берегите себя!
О СТАЛИ 95Х18Ш. Считается, что
главным критерием в подходе к ножу является
сталь. Позволю высказать "крамольную" мысль,
что это не совсем так. Мне кажется, что все-таки
конструкция - прежде всего. Встречаются
некоторые модели, в которых при изготовлении
используется сталь марки 95Х18Ш - сталь очень
мощная, но в тоже время и очень "капризная".
Применяется она при изготовлении нержавеюших
подшипников (на подшипниках из этой марки стали
стоит маркировка - "Ю"после номера).
Почему-то все, кому хочется иметь хороший нож,
начинают "отталкиваться" от этой марки
стали. Но незнание правильной технологии
термообработки или техническая неоснащенность
приводит к обратному результату. Я знаю немного
термистов, способных качественно провести
термообратку "95"-ой и получить заготовку с
заранее необходимой твердостью. При малом
сечении режущей кромки происходит
"крошение", что влечет за собой определенные
неудобства вплоть до потери экземпляра.
Приходится увеличивать сечение у режущей кромки
, и это приводит к снижению "правочной"
способности. Естественно, править такой нож
гораздо труднее, и "изготовитель" снижает
твердость по Роквеллу до 48-50 ед. Комментарии
излишни...
О СТАЛИ 65Г. Неплохие
ножи получаются из стали 65Г... к сожалению она
сильно ржавеет. Режущие свойства у нее
великолепны. Но участились случаи жалоб на ножи
из этой марки. Порой бывает - и отковал, и оттянул,
а "оно" не режет или, навареная на мясницкую
тупицу, не рубит. Я начал искать причину и одну
нашел.
Кустарям и разным "умельцам" 65Г доступна в
виде рессоры. Все изделия производятся в
основном из того , что добыто... на бескрайних
просторах нашей странной (от слова "страна" -
прим.автора) свалки металлолома и
некондиционного оборудования. Какое-то время я
работал кузнецом на автобазе , и доступ к этому
материалу у меня был неограниченный. Каждое утро
на "промежуточном" складе для моих нужд
находилось по 1-2 рессоры со сломанными листами. В
мои обязанности входило принести их в кузницу и
разобрать. После переборки добавить полученные
со склада новые листы, все это дело грамотно
отрихтовать, собрать и отправить обратно на
"промежутку" для дальнейшего оборота.
Кому-то покажется, что я очень долго и нудно
описываю всю процедуру ремонта рессор, но
поверьте - это необходимо. Может быть, Вы избежите
очень много неприятных моментов. За 10-15 лет
работы автомобиля все агрегаты у него
практически "не родные", а рессоры - тем
более. Более того, у самой рессоры листы, как
историческое обозрение. Одна передает привет из
60-х, другая из 80-х и так далее... Что же произошло?
То ли наука двинулась вперед и стали ставить
хилые заменители, то ли вода тогда была мокрее, но
факт остается фактом - листы из рессор
изготовления после 70-го лучше не использовать. Я,
например, вообще перешел на вагонные пружины -
гарантия практически 100%. Но для подстраховки
можете использовать стандартный лист со всеми
маркировками и атрибутикой. Да и ковать его не
надо. Правда, без ковки не хватает одной
"изюминки", но об этом мы, возможно,
поговорим далее...
МОДЕЛЬ. Могу предложить
к производству начинающим простую, но уже хорошо
зарекомендовавшую себя модель. Первый раз я ее увидел на
итальянской выставке. Поразившая меня своей
простотой и скромностью, она надолго отвлекла
меня от других изысканий. Итальянская фирма
"KAYMANO" создала действительно удивительный
образец. Проще ничего не бывает: рукоять и клинок.
Признаюсь, я влюбился в эту модель. И после
недолгих раздумий решил повторить ее. Отсутствие
такого образца у наших поваров и продавцов
морально угнетало меня. Но как решить проблему
оборудования? Ведь для изготовления клинка со
ступенькой требуется прецизиозный (особо точный)
плоскошлифовальный станок. Даже два. Один станок
обрабатывает клинок только с правой плоскости,
другой-с левой... Таких денег у меня не только на
станок - на документацию к ним (да и теперь нет)!!!
Но делать нечего, охота пуще неволи, как
говорится. Пробовал крупным "желобом"-
бесполезно. На широких (больших поварских)
клинках этого не добиться. Не хватит диаметра
абразивного круга, чтобы за один проход
захватить сразу 50мм по плоскости. Да и желоб для
профессионального ножа - невыигрышный элемент.
Поварскому клинку требуется вес и достаточная
жесткость. При нужной нам конструкции желоб
снимет весь необходимый для веса и жесткости
металл. И сие будет означать, что цель не
достигнута. Потом меня осенило - можно ведь снять
лишнюю массу аккуратно при помощи оправки, т.е.
специального приспособления или устройства. Это
устройство должно нести на себе обязанность
ограничителя. И не допустить вращающийся
наждачный круг к полированной ступеньке. Как
только я до этого додумался...через полчаса
сделал первую оправку. Она состояла из двух
пластин с точно рассчитыннами отверстиями (как и
на хвостовике клинка) под заклепки. Плюс еще
набросил от "пятки" клинка 20мм на ступеньку.
Эффект был для меня радостным. Немедленно
приступил к изготовлению полудюжины ножей.
Однако до полной отработки технологии было еще
далеко. Доставляло немало хлопот совмещение
отверстий под заклепку во-первых, а во-вторых и
сами отверстия мне пришлось сверлить в
хвостовике диаметром 4мм. Крепление-то пластин
к клинку производилось двумя болтами с гайками
М4. И при заклепке диаметром 3,5мм это несколько
неудобно. Приходится "напрягаться" при
расклепывании - как бы не расколоть ручку, как бы
не было шатания в месте соединения. Короче
говоря, пожертвовал временем ради качества - стал
оправку из двух пластин приклепывать к
хвостовику, а потом, чтобы снять оправку,
стачивать заклепки. "Дурдом" конечно, но на
том этапе и это было уже достижение. Технология
малопроизводительная, но кустарю этого
достаточно. Позже руководство Московского
завода "СТИЗ" попросило меня доработать эту
технологию для производства. Вот тогда-то я и
решил эту проблему с оправкой. Я просто согнул
вдвое пластину толщиной 1,5мм, и, просверлив
отверстие 6,5 мм, стал крепить оправку болтом с
гайкой М6 под хвостовиком. Проблема с оправкой в
данной модели была решена. Позже я стал
использовать данное приспособление при
изготовлении и других конструкций, немного
изменив оправку.
На снимках сверху -
заготовка разделочного ножа в оправке, снизу -
поварской нож для мяса.
НОЖИ СПЕЦИАЛЬНЫЕ. Пожалуй самыми
сложными в изготовлении , как мне кажется - ножи
специальные. Ну столько к ним предьявляется
условий, что порой, бывает, одну-две заготовки
загубишь, пока не начнет получаться желаемое.
Среди таких ножей - обвалочные. В этой группе я
знаю несколько моделей. Они различаются как по
способам изготовления, так и по внешнему виду.
Требования к режушим свойствам и формам в этой
категории настолько высоки, что иногда начинаешь
подозревать мясников-обвальщиков в занудности и
капризности. Но все подозрения рассыпаются в пух
и прах , когда поближе познакомишься со
спецификой этой замечательной профессии. Порой
по 12 часов нож в работе... И если
мастер-изготовитель не постарался, поминают его
почем зря... Впрочем не очень долго. От таких
изделий обычно избавляются быстро. С прискорбием
признаю - я не исключение. И мне приходилось
выслушивать нелестное... Но меня миновала большая
часть сберегаемого словарного запаса на этот
случай. Причина в том, что я, желая понять, в чем
кроется секрет обвалочного, использовал
нехитрый прием. Прежде чем сделать свой первый
"обвальник" на продажу, я заимел трех
"экспертов". Два из них работали в
близлежащем магазине, третий - муж моей
одноклассницы, носящий дивную фамилию Максичка
(сейчас, кстати, в Москве можно встретить в
продаже полуфабрикаты его производства).
Безвозмездно было изготовлено и роздано
несколько ножей с тайной надеждой на похвалу... Не
тут-то было. Полный провал... Даже за бесплатно. Но
не буду утомлять описанием свих опытов и
переделок (а их было на протяжении полугода
несколько) , а сразу дам советы тем, ктопойдет по
пути создания обвалочных ножей. Ищите золотую
середину в конструкции клинка ... Не скупитесь на
приобретение лучшего сырья... Сделайте
обвальщику на выбор пару ножей...Отдайте ему их в
работу на 2 часа и погуляйте. Если вам вернут ножи,
не переживайте. Этого не избежал никто из
применяющих подобную практику. Если вам
приготовили оговоренную сумму за один нож- смело
приступайте к изготовлению ножей, продадите
практически все. Если вы получите деньги за оба
ножа ... Вы - ГЕННАДИЙ КОНСТАНТИНОВИЧ (ШУТКА) !!!
Один из секретов
или одна из хитростей. Необходим материал,
способный хорошо науглероживаться. Можно
использовать сталь марки 40Х. Изготавливаете
изделие до предшлифовочного состояния.
Цементация на 0,1-0,2 мм. Термообработка. Шлифовка. В
итоге: вязкая сердцевина в науглероженой
оболочке твердостью до 60 ед.по "Роквеллу"
Обвальщики очень благодарны. При
соприкосновении с костью два твердых слоя ,
несущие основную нагрузку, ведут себя
восхитительно. Практически ИДЕАЛЬНО.
Хороших, но очень
дорогих (включая дамаск) я за всю свою
деятельность сделал всего 7 штук. Знаю, где они
находятся, у кого, и в каком состоянии. Просто
дорогих и простых я не прослеживал (к моему
сейчас сожалению). . . . . .
УВЛЕЧЕНИЯ. В особом ряду стоит
свободное время. Практически все
неиспользованные задумки и фантазии,
пришедшие в голову, я стараюсь воплотить в
экзотических изделиях, или в изделиях, которые
расходятся на "подарки". Хотя всегда
происходит так, что именно после полета фантазии
и появляется что-то такое, что приносит мне
необъяснимую радость и чувство глубокого
удовлетворения. Так произошло с ножом, который у
меня заказал один из моих друзей для сувенира
некоему гурману..
Первоначально нож задумывался, как милая шутка,
хотя и несколько "черноватая". Изделие имело
первоначальное название "Сувенирный
кухонный нож для для харакири, многоразового
использования". А в итоге появился -
"ТАНТИК". Разделочный нож для дичи и рыбы в
японском стиле.
По заказу одной турфирмы, для выставки во Франции
было изготовлено несколько ножевых изделий
"рыболовного профиля" из дамасской стали. К одному из ножей были предъявлены
очень высокие требования. Во-первых плавучесть
(нож не должен тонуть). Во-вторых, очень быстро
восстанавливать свои режущие свойства
(требование к промысловым ножам). В-третьих,
конструктивные особенности должны позволять
ножу выдерживать кратковременный изгиб клинка
до 80о . И так вышло, что этот заказ делался в
трех местах. Я делал клинок, в другом месте
высококлассный мастер изготовил рукоять и
соединение (крепеж). В третьем был изготовлен
кожаный чехол - точно подогнанный под форму ножа.
Этим бы ребятам не
только турпоездками заниматься, а объединить бы
нас всех, разбросанных по России, хотя бы в
изделиях... "Мы бы еще поглядовали, у какой
сторонушки нож ножистее".
ИТОГ: Рыболовный филейный нож - "ПУТИНА -
1";"ПУТИНА - 2";"ПУТИНА - 3".
на снимке: рыболовная пара
(ПУТИНА-3","СКИНЕР-С"). |